Project Description
The Project
InfraSteel, a permanent culvert rehabilitation system, was identified by the Tennessee Department of Transportation to slip-line a deteriorating corrugated metal pipe (CMP) culvert under State Highway 242 in Lawrence County, TN. Hwy 242 is the main paved state access through the south-central county, and Region 3 Maintenance Engineers determined that slip-lining was the best option for repairing the failing structure. The alternative of cutting and replacing the roadway would have resulted in a significate detour of local residents as well as emergency vehicles in the area.
The InfraSteel team first met with the TDOT Region 3, Maintenance Engineers in the summer of 2019 to discuss InfraSteel’s capabilities and benefits as a smooth wall, carbon steel, culvert slip-liner. Following this initial meeting the two organizations conducted a thorough site inspection to assess current conditions and feasibility of a slip-line rehabilitation in September 2019.
The Challenge
Initial inspection of the structure revealed that severe deterioration of the invert had occurred due to abrasive and corrosive factors in the environment, and the length of time that the culvert had been in service, which was estimated to be 50+ years. In order to secure streamlined procurement for the liner, the InfraSteel team worked with the Tennessee Department of Transportation Materials and Test office to certify InfraSteel as an approved liner option.
With the InfraSteel liner identified as the preferred rehabilitation option, the team set to work confirming the interior dimensions of the culvert, and the design of the InfraSteel liner. Detailed measurements and survey were taken to ensure the liner would match the exact shape of the existing structure, and maximize the area of flow.
This major sizing consideration took into account the hydraulic capacity of the liner. With a manning’s coefficient of .012, InfraSteel provided a greater flow rate than the existing CMP culvert. Inlet & Outlet control features were also available but not required on this project. Upon confirmation that the designed liner would meet all site and project requirements, InfraSteel fabricated a metal template and shipped to the project site in February 2020. This template was assembled by TDOT Maintenance Crews and walked through the structure ensuring a proper fit, and verifying no complications would arise once the lining commenced.
The InfraSteel liner was then entered into production and shipped to TDOT’s Lawrenceville Maintenance yard in March 2020. With the liner shipped in 8 pieces, each measuring 8-10ft in length, TDOT decided to weld two sections together in order to save on the number of field welds required at the project site. During this time TDOT prepared the site for rehabilitation by cutting and removing the deteriorated invert, and pouring a concrete pad with inserted channel iron in order to facilitate an easy slip-line insertion.
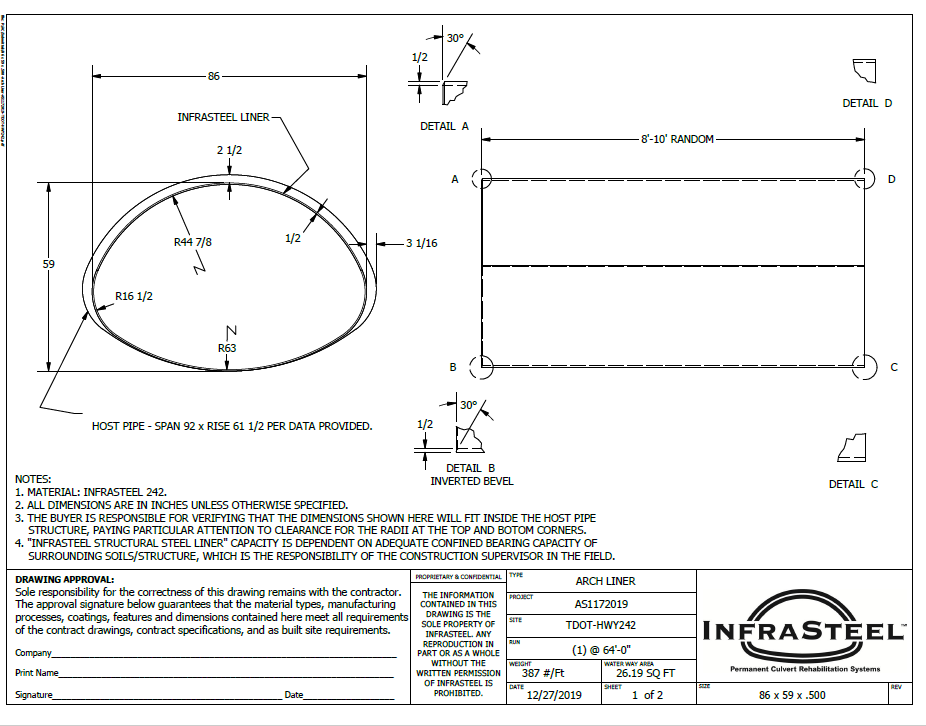
The Solution
TDOT Maintenance crew’s cut and removed the deteriorated invert, and prepped the existing culvert for slip-line rehabilitation by pouring a concrete slab and laying channel iron for the InfraSteel liner to slide over. Once the concrete slab had cured, the InfraSteel liner sections were transported to the site in August 2020. An excavator was brought on site to move and position each liner section into place. TDOT utilized maitnenace and welding crews to join the liner sections together with full penetration welds, ensuring no possibility of joint failure. The liner was then pushed into the existing structure.
The liner section contained inverted bevels on the bottom of each seciton, allowing for welding to occur inside the liner. Welding of the top of the liner was accessible from the outside. A look inside the liner shows crossing bracing that is tac-welded into place ensuring each section keeps its shape during transportation. The cross bracing also serves as a “crosshair” when aligning the sections into place. These are left in place until the grouting process of the annular space is complete. (They can be removed if manipulation of the ends is required to ensure alignment of full penetration welds.)
Once the liner was pushed into place, TDOT proceeded to utilize pressurized grout to fill the annular space between the InfraSteel liner and existing structure. The end result is a new structure that will continue to serve the Volunteer State for another 70+ years. More than just a component of the highway infrastructure, culverts or groups of culverts, serve an important purpose to carry drainage water from one side of a roadway to another; in addition, they also serve a bridge function to transport the traveling public across waterways. They can be found with round, boxed, elliptical, or arched construction. The overall condition of the approximate 4 million miles of culverts across the country varies, but many have been in service for 30-70 years and are reaching the end of their designed service life.
This need has led to the growing market of trenchless rehabilitation. It is now possible to fully rehabilitate or repair a structure with no impact to the roadway or traveling public. According to a recent article by Trenchless Technology, “State and local governments have become more aware of and are utilizing trenchless rehab methods for repairing their aging and deteriorated culvert and drainage systems…currently, the rehabilitation of storm water pipelines and culverts is estimated to be 15 to 20 percent of the overall trenchless rehabilitation marketplace.”
States and counties with active culvert inspection programs are less likely to experience a catastrophic failure or roadway collapse.
It is as equally important for all infrastructure professionals and traveling public to be aware, and on the lookout, for the common signs of an impending culvert failure. Many potential failures can be identified from the roadway surface by paying attention to the tell-tale signs of pavement cracking, eroding embankments, and dips or drops in the road and guardrails where there are creeks or streams.