Resources
InfraSteel Slip Lining Process
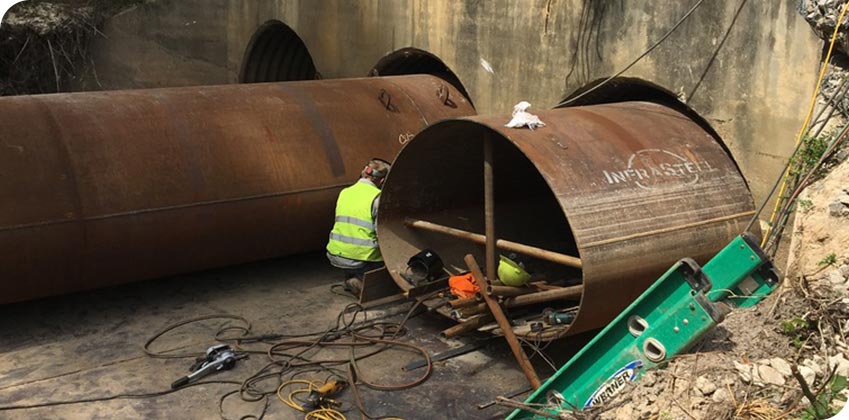
Slip lining with InfraSteel is a safe, environmentally friendly, and structurally superior way to rehabilitate failing culverts. We provide a template of the determined liner shape and size, for the installer to pass through the existing structure, and to help line up the installation process.
Understanding the slip lining process is crucial to ensuring the successful installation of your culvert liner. The slip lining installation procedure involves carefully inserting a new pipe into the existing one, offering an effective solution for pipe rehabilitation. At InfraSteel, we take pride in providing comprehensive guidance on the culvert liner installation procedure. Our slip line pipe installation process enhances durability while also ensuring minimal disruption to the surrounding environment. As part of our commitment to customer satisfaction, we also provide tailored advice on the slip lining process to suit the specific needs of each project. Trust InfraSteel to deliver industry-leading services and support for your slip lining installation needs.
- When lining up the joints for welding, the critical alignment points are the longitudinal weld seams, and the 2 tangents points in the bottom where the flatter bottom radius transitions to the tighter haunch radius. The bracing inside of the liner should be used only as a visual tool to aid in alignment; think of aligning the crosshairs of a scope when setting the pieces into position.
- To aid with alignment, Ears or Tabs should be welded on the top of the end of one piece, so it can be hung on the piece it is being aligned with.
- Porta Power tools, wedges and modified C clamps should be used by the welders for manipulating the steel to make the ends of each section match prior to welding. Begin by tack welding the pipe every 6 inches once it is aligned. The welders should start welding at the invert, and then work upwards to the 12:00 position. The top radius is typically the best place to adjust any slack in the steel.
- The cross bracing should be removed during the manipulation of the ends for welding. This allows the liner to flex slightly and the walls to fit up flush. Replace 1 set of cross bracing at each joint area during the grouting process.
- Grout Ports should be added every 10’ at 12:00, 3:00, and 9:00. As grout is being pumped into the downstream end the grout will fill up the annular space moving up hill. As the grout moves uphill the next grout port will be used as a vent or window, to determine the position of the grout, and should be plugged when grout reaches it. Grout ports should be used as needed and can be added anywhere that grout is needed to fill voids. Grout pressure should not exceed 3.5 psi at point of injection.
- Tapered or conical lead sections are available. This allows liner section to be forced through sections of the host structure that have movable obstructions. Tracks or rails may be welded to the bottom of the host pipe to reduce the resistance and force required to slip the liner through the host.
- Arched liner with a flat bottom is more prone to float when grout is being pumped than pipe with a radius on the bottom. If necessary, spacers may be added to keep the liner from floating, prior to grouting, by cutting a hole in the top of the piece, and welding in a steel spacer that runs from the top of the liner to the ID of the host pipe structure. Grouting should be done in 2 or more stages.
- Liners are assembled and welded together by two methods: Method 1 is fitting the liner sections together outside of the host, and then slipping the liner into the host. Method 2 is loading each liner section inside the host, and fitting the joints from the ID. The installer is required to advise InfraSteel of the lining method chosen, and specify the end bevel configuration of the liner.
Limited Warranty: InfraSteel is manufactured for each specific purchase and is warranted only to the extent that it is proven to be defective in material or workmanship prior to installation. Damage due to installation or grouting is not warranted. If the product is deemed defective, the purchaser should provide immediate written notice of the defect and provide an opportunity for inspection by an InfraSteel representative. The InfraSteel product will be repaired on site, repaired at the plant, or replaced at InfraSteel’s discretion, to the satisfaction of the purchaser.